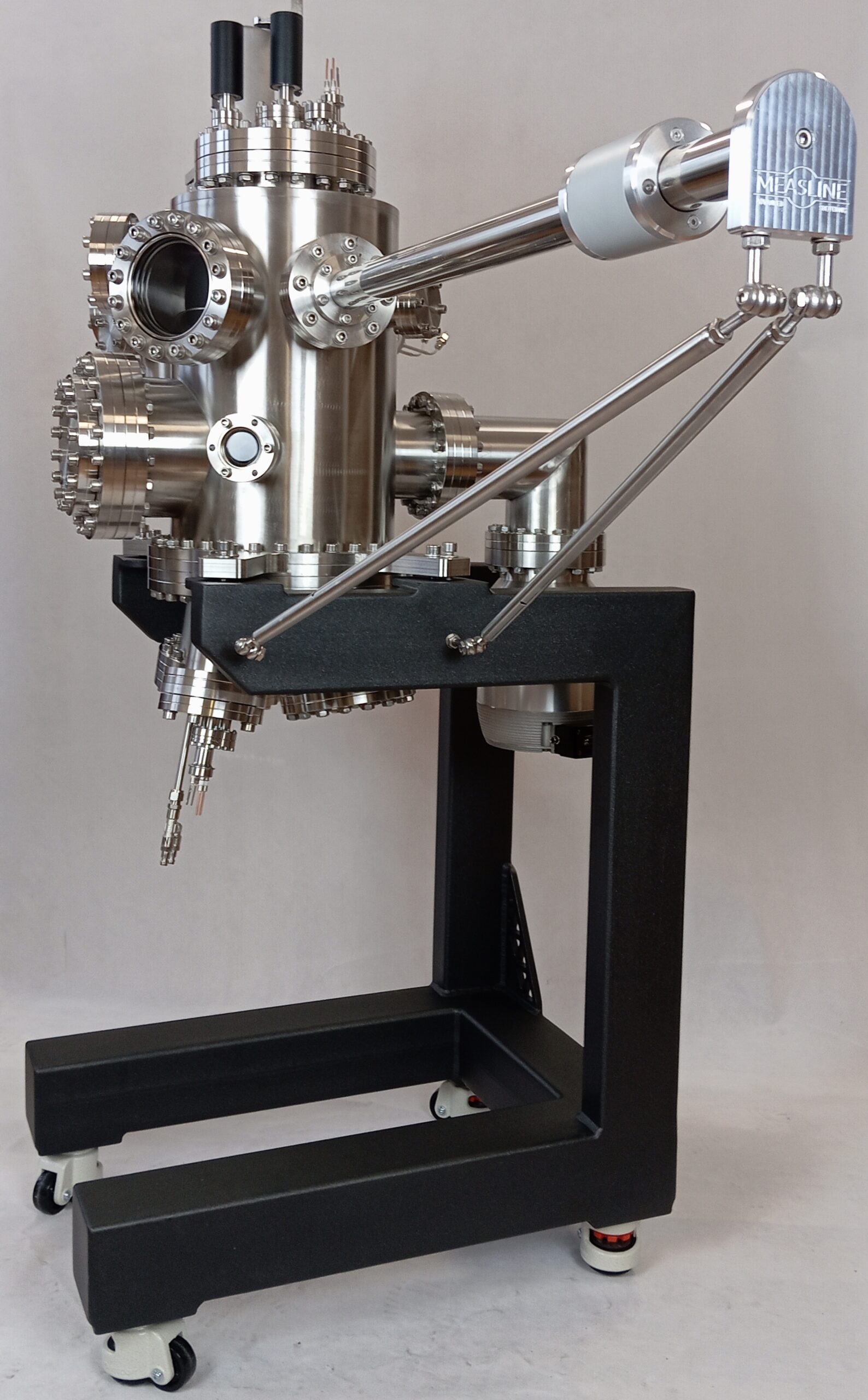
Sputtering system dedicated to TERS Tip Coating
The thermal deposition chamber is built to UHV (Ultra-High Vacuum) standards. It is designed to accommodate up to four thermal evaporators with a vacuum-access window that allows material to be added to the evaporators without breaking vacuum. The thickness of the deposited layers is monitored using a quartz crystal microbalance (QCM).
The system is equipped with a sample holder specifically designed for mounting AFM probes, enabling the deposition of uniform coatings on TERS (Tip-Enhanced Raman Spectroscopy) tips.
Uniformity of the deposited layers is ensured by a rotating stage that provides continuous rotation of the sample holder during deposition. The stage is capable of heating the sample and maintaining a stable temperature in the range from room temperature up to 400°C. Moreover, the sample heating and rotation station has a sample shield.
The sample holder, with the mounted samples, is transferred from the the load-lock chamber to the thermal deposition chamber using a linear transfer system, ensuring that the vacuum in the deposition chamber remains stable during the transfer process. Once the holder is placed in the loading chamber, the chamber can be pumped down to the required vacuum level, and then the valve separating the loading chamber from the deposition chamber can be opened.
The deposition system also supports a holder for mounting various other samples with a maximum size of 50×50 mm. It is also possible to mount multiple smaller samples simultaneously.
The system can be expanded with a sample holder storage chamber that can store up to five sample holders under vacuum conditions.
The most significant device features:
- The thermal deposition chamber is built to UHV standards
- Specialized Holder Enabling Mounting of up to 10 AFM Probes
- A device dedicated to coating tips used in Tip-Enhanced Raman Spectroscopy (TERS) applications.
- The chamber allows the mounting of up to four thermal evaporators
- A vacuum window enables the addition of material to the evaporators
- The loading chamber is used for introducing samples under atmospheric pressure
- A linear transfer is used to transport samples from the loading chamber to the thermal deposition chamber
- The thickness of the layers is controlled using a quartz crystal microbalance
- The system allows sample heating up to 400ºC.
- The sample mounting station provides continuous rotation during the deposition process
- The pressure in the thermal chamber, below 10-6 mbar, is achieved after venting the chamber with dry air or nitrogen within 2 hours using a turbomolecular pump with a pumping speed of no less than 200 l/s. The base pressure after heating the chamber to 150ºC for 48 hours is <10-9 mbar.
- The loading chamber can be pumped using a dry pump to a vacuum below 10-1 mbar or by using a pumping station with a turbomolecular pump.
Specification:
Source of applied material | Up to four thermal evaporators |
Working temperature of evaporators | up to 1600ºC |
Crucible volume | 5 cm3 |
Layer thickness control | quartz scale |
Sample temperature | from room temperature to 400°C |
Time to obtain vacuum |
10ˉ⁶ mbar within 2 hours of chamber aeration |
Pump system |
turbomolecular with pumping speed >200 l/s dry fore pump with a pumping speed of not less than 5 m³/h |
See also other thin-layer deposition systems:
Compact sputtering system LPNW01 for thermal deposition of thin layers
PVDS 700 Coating deposition system for layer deposition with the PVD technique
Magnetron system for coating deposition MCS 787 equipped with up to four magnetron sources.
Compact sputtering system for surface metallization with the possibility of thermal and magnetron deposition of layers